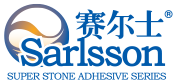
Hotline:
133-3102-1811
Chinese
News
首页 > News > Industry information >
Silicone sealant used in the process of bonding is not good? The reason is it!
Date:2020-09-06 09:40:00
Share:
With the development of these decades, the use of silicone sealant has been involved in curtain wall, doors and windows, automobile, road and bridge, new energy, electronic appliances, aerospace, electric power and environmental protection and many other fields. Silicone sealant with its excellent weather resistance, a wide range of temperature, appropriate physical and mechanical strength, long service life and other advantages in the adhesive industry.
As a kind of adhesive, good adhesion is essential. But in the actual use process, occasionally there will be poor bonding problem, let's take a look at what causes this phenomenon?
1. Is the product selection correct?
Nowadays, the use of silicone sealant has been involved in many fields, and there will be many application points in different application fields. Silicone sealant can be divided into acid type, alcohol type and oxime type. Acid type adhesive has the advantages of rapid surface drying and deep curing, but it will release acetic acid molecules in the curing process, which has a strong taste, and will corrode some base materials, such as concrete and metal; the advantages of alcohol type adhesive are neutral curing, the released alcohol molecules are non-toxic to the body, and can be bonded to the substrate widely, but the disadvantage is that the deep curing is not as good as the acid type adhesive; the oxime type adhesive has the advantages of neutral curing, and the released alcohol molecules are non-toxic to the body It has the advantages of neutral curing, deep curing faster than alcohol type adhesive, and can bond to the substrate widely, but it will corrode copper materials. Therefore, the chemical system of different types of silicone sealant is different, and the way of forming adhesion is also different. If you want to form a good adhesion, you must choose the appropriate product.

2. Is it a special substrate?
With the rapid development of the material industry, many new materials are widely available. A silicone sealant can not guarantee good adhesion to all substrates; even if the same substrate is used, different surface treatment methods will make the bonding effect of silicone sealant different; even if the same treatment method is used, the bonding effect of different manufacturers and batches of materials is quite different. In this context, it is strongly required to carry out the adhesion test before the use of silicone sealant, so as to select the appropriate product, cleaning agent and primer.
3. Is the cleaning process followed?
The two cloth cleaning method consists of first wiping with a cotton cloth soaked with solvent, and then wiping with a second clean cloth. Note that white, clean, soft and lint free cotton cloth should be used in the process.
① Thoroughly remove all loose residues on the substrate surface.
② Pour some solvent of appropriate cleaning grade on cotton cloth. Organic solvents are best packed in plastic bottles that can be extruded (solvent resistant). Do not immerse the cotton cloth directly in the container containing the solvent, because the dust on the cotton cloth will contaminate the solvent.
③ Wipe the surface of the substrate with force and check the rag to see if the surface dirt is removed. Wipe with a clean place on the cotton cloth in turn until no dirt is adsorbed on the cloth.
④ Immediately wipe the solvent and residue on the substrate with another piece of completely clean cotton cloth. Before volatilization, the organic solvent must be dried with dry cotton cloth, otherwise the cleaning effect will be reduced. Some porous materials may have a little residual solvent on the surface of the substrate. In case of this situation, it is necessary to wait for the surface substrate to dry before installing the backing material and applying sealant.
⑤ Isopropanol and methyl ethyl ketone can be dissolved in water, so it is very suitable for use in winter. It can effectively remove the condensation water and frosting on the surface of the substrate. Toluene and xylene are not soluble in water, so they are more suitable for use in summer.
Note: do not touch the surface to see if it is dry after cleaning.
4. Is the primer applied correctly?
The role of primer is to promote the adhesion between sealant and substrate. Proper use of primer will help to produce strong and continuous adhesion to the surface that is not easy to bond. Before using the primer, the surface of the substrate should be dry and clean; when using, a clean, lint free cotton cloth should be used to coat a thin and uniform primer on the interface surface. If it is difficult to apply or rough surface, a brush can be used. Do not pour or use the primer too much. After use, silicone sealant should be used after the primer is completely dry.
5. Is the injection full?
In order to meet the expected performance requirements, the silicone sealant needs to be fully filled at the designed interface, and the width and thickness meet the interface design requirements. At the same time, it also needs to use a scraper to make the colloid fully contact with the substrate to form an effective bond. The correct sizing should be uniform and continuous, and then be modified with a scraper within the operating time range. During the modification, efforts should be made to make the colloid have a good contact with the surface to be bonded.
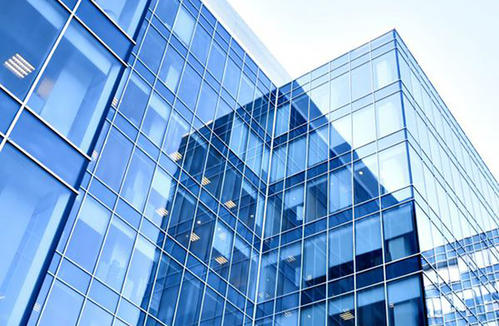
6. Is the curing time sufficient?
According to GB 16776-2005 silicone structural sealant for building, the two-component silicone structural sealant shall be cured for 14 days under the standard test conditions (temperature 23 ℃ ± 2 ℃, humidity 50% ± 5%), and the single component silicone structural sealant shall be cured for 21 days under the standard test conditions (temperature 23 ℃ ± 2 ℃, humidity 50% ± 5%).
The performance of silicone sealant is reflected after its complete curing, and the bonding is gradually formed during the curing period. The bonding test should also be conducted after the curing period. In addition, it should be noted that the 21 days and 14 days for single and double components mentioned above are the curing period under standard test conditions. If the temperature is low or the humidity is low, the curing period should be extended appropriately.
Through the inspection of product selection → special base material → cleaning → primer → gluing → curing process, most of the problems of poor adhesion can be solved, but some special cases can not be ruled out. At this time, we can contact the technical personnel of silicone sealant manufacturer for analysis and solution.
Copyright © 蚌埠赛尔时代工贸有限公司 皖ICP备17024280号
技术支持:智导互联